WHY IS EN469 SO IMPORTANT ?
We provide an explanation for the latest revision of the EN 469
We provide an explanation for the latest revision of the EN 469:2020 standard in relation to protective clothing for firefighters and expect to help wearers, organiztions and buyers of PPE fully understand the meaning of these tests which correspond to the disaster relief.
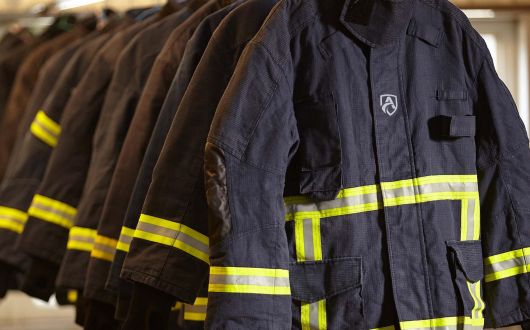
Provide Premium Products to Worldwide
We provide an explanation for the latest revision of the EN 469:2020 standard in relation to protective clothing for firefighters and expect to help wearers, organiztions and buyers of PPE disaster relief.
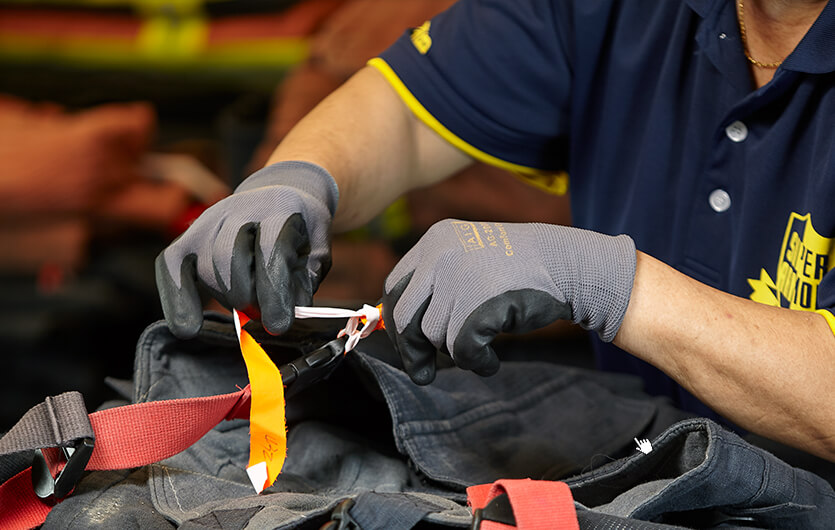
EN469 TEST
METHOD
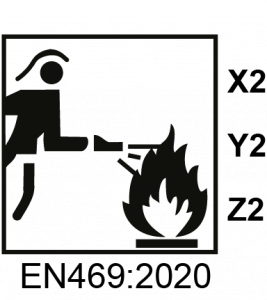
Performance levels:
.Level 1
Lower level of protection which meets the minimum performance requirement of outerdoor firefighting and peripheral support operation.
Not applicable to structural firefighting and the risk that the wearer may face in the firefighting.
.Level 2
Higher level of protection which meets the minimum performance requirement of structural firefighting and disaster relief operations.
When there are both level 1 and level 2 performance in the heat and flame protection section of a firefighting suit, the suit should be classified as level one and not allowed for structural firefighting. The wearer and purchaser should select firefighting suits at the suitable protection level based on disaster relief risk assessment.
Property | Performance Marking | |
Level 1 | Level 2 | |
6.2.1.2 Contact heat | No required | X2 |
6.2.1.3 Heat transfer (flame) | X1 | X2 |
6.2.1.4 Heat transfer (radiation) | ||
6.2.4 Water penetration | Y1 | Y2 |
6.3.1 Water vapour resistance | Z1 | Z2 |
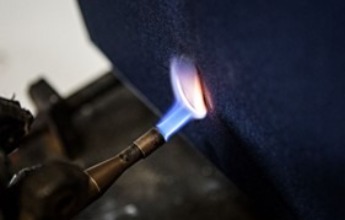
The material shall be tested by applying the test flame to the surface for 10 seconds to stimulate the accidental flame contact in a fire scene.
Need to meet below requirements in order to protect wearers effectively.
Tested material | Test method | EN 469:2020 test requirement |
Outer materials | EN ISO 15025 | .EN ISO 14116 index 3 .No flaming to edge .No hole formation .No flaming or molten debris .Afterflame ≦ 2s .Afterglow not to spread |
Innermost lining | ||
Seams | ||
Wristlet materials | ||
Hardwear | ||
Larger labels |
It happens that firefighters must stay low and crawl on the floor to escape the threat of smoke. When the floor temperature reaches 250°C, how long time could firefighters' elbow and knees withstand such high temperature?
Contact Heat is only required for Level 2 garments.
The test is executed before and after pre-treatment by 5 times washing. Test method is EN ISO 12127-1:2015. When the contact temperature reaches 250°C, the time it takes for the "inside" temperature of the assembly to rise by 10°C is measured. And the time required is at least 10 seconds.
Contact heat testing requires the time at least 10 seconds. The longer the firefighting suit lasts for testing, the more safety the firefighting suit provides to firefighters.
Property | Pretreatment | Performance attribute 1 and Marking (where applicable) | Performance attribute 2 and Marking (where applicable) | ||
---|---|---|---|---|---|
Contact heat | Before & After | Tt -- | LEVEL X1 | Tt ≧ 10s | LEVEL X2 |
The test is executed before and after pre-treatment by 5 times washing. Test method is ISO 9151:2016, a method for determining the heat transmission through assembly materials used in protective clothing.
Speciman is exposed horizontally to an intensive heat flux of 80kW/m².
HTI12 is the time to reach temperatures associated with first degree burns of human skin (PAIN).
HTI24 is the time to reach temperatures associated with second degree burns of human skin (BLISTERS).
HTI24-12 is the reaction time between +12°C and +24° C.
ISO 9151:2016 test indicates 2 performance levels in the EN 469:2020 :
X1 - the lower performance level
X2 - the higher level.
Firefighters are often exposed to confined environments with extremely high temperature which might be the heat emitted by direct flame. When they feel pain (usually the back skin), it's an alert of first degree burns, they should prepare to evacuate before the temperature reaches second degree burns that paralyzes their mobility.
Important : The heat transfer index should not be taken as a measure of the protection time given by the tested materials under actual use conditions.
Property | Pretreatment | Performance attribute 1 and Marking (where applicable) | Performance attribute 2 and Marking (where applicable) | ||
---|---|---|---|---|---|
Heat transfer (flame) | before & after | HTI24 ≧ 9.0s HTI24-12 ≧ 3.0s |
LEVEL X1 | HTI24 ≧ 13.0s HTI24-12 ≧ 4.0s |
LEVEL X2 |
The EN ISO 6942:2002 test exposes the fabrics to an intensive radiant heat of 40kW/m2 and determines the values of the RHTI12 (first degree burns) and the RHTI24 (second degree burns) and those of the RHTI24-12 as reaction time.
The EN ISO 6942 indicates 2 performance levels in the EN 469:2020 :
X1 - the lower performance level
X2 - the higher level.
Firefighters are often exposed to confined environments with extremely high temperature which might be the heat convected by burnt substances. When they feel pain (usually the back skin), it's an alert of first degree burns, they should prepare to evacuate before the temperature reaches second degree burns that paralyzes their mobility.
Important : The heat transfer index should not be taken as a measure of the protection time given by the tested materials under actual use conditions.
Property | Pretreatment | Performance attribute 1 and Marking (where applicable) | Performance attribute 2 and Marking (where applicable) | ||
---|---|---|---|---|---|
Heat transfer (radiation) | before & after | RHTI24 ≧ 10.0s RHTI24-12 ≧ 3.0s |
LEVEL X1 | RHTI24 ≧ 18.0s RHTI24-12 ≧ 4.0s |
LEVEL X2 |
Why this evaluation is necessary?
It ensures firefighting suits remain durable after exposure to intense radiant heat. This provides firefighters with a break-resistant barrier, reducing the risk of burns or injuries and ensuring reliable performance in high-stress, life-threatening situations
It guarantees that the firefighter suits won't compromise the wearer's safety when they are exposed to extreme heat, allowing them to focus on their mission.
The EN ISO 6942, Method A is used to simulate radiant heat exposure, while the residual tensile strength is tested using EN ISO 13934-1. Each specimen must retain a minimum tensile strength of 450 N to pass this requirement.
Property | Pretreatment | Test Method | Requirement |
---|---|---|---|
Residual tensile strength of material when exposed to heat |
after |
EN ISO 6942:2002, Method A, at a heat flux density of 10 kW/m2. |
Tensile strength ≥ 450N |
EN ISO 13934-1:2013 for woven textiles |
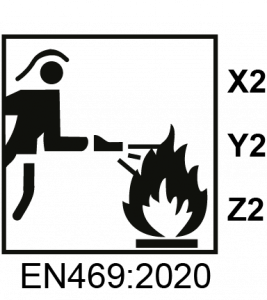
6.2.1.6 Heat resistance
When tested according to ISO 17493:2016 at a temperature of (180 ± 5) °C for an exposure time of 5 min, each material used in the garment assembly shall not ignite or melt and shall not shrink more than 5 % in either machine or cross direction. Each layer of the material shall be tested separately. If a specimen of sufficient size cannot be taken it may be fixed on the carrying material as used in the garment.
When tested according to ISO 17493:2016 at a temperature of (180 ± 5) °C for an exposure time of 5 min, hardware of the type(s) intended to be used in the finished garment, shall remain functional after this test. Five minutes after removal from the testing oven any closure system for doffing shall be capable of being opened once.
ISO 17493:2016, Clothing and equipment for protection against heat - Test method for convective heat
resistance using a hot air circulating oven
Property | Pretreatment | Performance attribute 1 and Marking (where applicable) | Performance attribute 2 and Marking (where applicable) |
---|---|---|---|
Heat resistance | before | shrinkage ≤ ± 5 % No ignition No melting Requirements also for slide fasteners and hardware |
Firefighters often encounter hazardous substances during emergency responses, including chemicals from burning materials, spills, or contaminated firefighting water. Exposure to these substances poses serious health risks, such as chemical burns, respiratory issues, skin irritation, and long-term conditions from toxic absorption.
By meeting EN ISO 6530 standards, firefighting suits are designed to repel or minimize the penetration and absorption of hazardous liquids, providing essential protection for the firefighter's safety.
Property | Pretreatment | Test Method | Requirement |
---|---|---|---|
Resistance to penetration of chemicals |
after | EN ISO 6530:2005 | No penetration to innermost surface. Repellency rate > 80% |
Tensile and tear strength are essential for firefighting suits as they directly contribute to the suit's durability and ability to withstand physical stress.
High tensile strength allows the fabric to resist stretching and breaking under force, while tear strength ensures that the material won’t rip easily when subjected to sharp objects or rough conditions.
Together, these properties help maintain the suit’s structural integrity, ensuring it stays intact and functional during intense firefighting operations. This is vital for providing continuous protection, as a compromised suit could leave the firefighter vulnerable to injury.
Property | Pretreatment | Test Method | Requirement |
---|---|---|---|
Tensile strength (Outer material) |
After | EN ISO 13934-1:2013 | ≥ 450N |
Tensile strength (Outer seam) |
After | EN ISO 13935-2:2014 | ≥ 300N |
Tear strength (Outer material) |
After | EN ISO 13937-2:2000 | ≥ 30N |
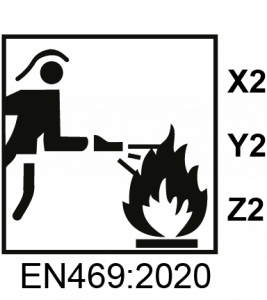
6.2.4 Water penetration (Marked with Y1 or Y2)
Five specimens of any layer [including seams] providing the resistance of water entry, when tested after pre-treatment in accordance with EN ISO 811:2018 using a rate of increase in pressure of (0,98 ± 0,05) kPa/min shall achieve one of the following performance grades:
EN ISO 811:2018, Textiles - Determination of resistance to water penetration - Hydrostatic pressure test
- Y1 < 20 kPa, for garments without a moisture barrier;
- Y2 ≥ 20 kPa, for garments with a moisture barrier.
Test specimens shall be taken from critical areas e.g. shoulder seams.
Property | Pretreatment | Performance attribute 1 and Marking (where applicable) | Performance attribute 2 and Marking (where applicable) | ||
---|---|---|---|---|---|
Water penetration (Grade) | after | < 20 kPa | Y1 | ≥ 20 kPa | Y2 |
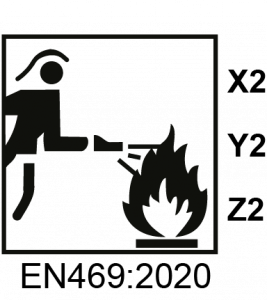
6.2.5 Dimensional change
Changes in dimension due to cleaning of material for protective clothing shall not exceed ± 3 % for woven materials and ± 5 % for knitted material and nonwovens in either length or width.Dimensional changes shall be tested according to and meet the requirements of EN ISO 13688:2013 using one specimen of the combination of materials in the component assembly.
EN ISO 13688:2013, Protective clothing - General requirements
The combination of materials in a component assembly shall be prepared so that all the layers of the material are sewn together around all four edges of the test specimen. One test specimen shall be tested. Pre-treatment will be carried out as an assembly. Once completed, all components will be separated and measured individually.
The test on performance of the component assembly shall not be performed if each single layer of the assemblymeets individually the dimensional change requirements.
Sizing should take into account the expected shrinkage and the expectation that clothing will be worn underneath the EN 469 garment (e.g. summer and winter time).
Property | Pretreatment | Performance attribute 1 and Marking (where applicable) | Performance attribute 2 and Marking (where applicable) |
---|---|---|---|
Dimensional change | after | ≤ ± 3 % (woven) ≤ ± 5 %(non-woven and knitted) |
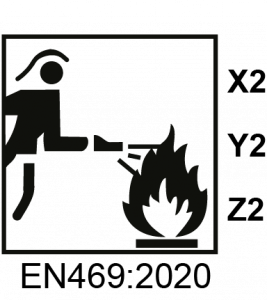
6.3.1 Water vapour resistance (Marked with Z1 or Z2)
The requirements for water vapour resistance (Ret) shall be achieved by testing three specimens after pre-treatment of either the component assembly or the (multilayer) garment assembly. Anti- wicking barriers, retro-reflective, fluorescent or combined performance material(s) are excluded from this requirement.
NOTE 1 Accessories such as anti-wicking barriers, retro-reflective, fluorescent layers, labels or pockets can reduce the water vapour transmission.
NOTE 2 Annex E provides another test method on physiological impact – sweating torso that will provide additional information on comfort.
Testing shall be in accordance with EN ISO 11092:2014 and one of the following performance grades shall be achieved:
— Z1 > 30 m2 Pa/W, but not exceeding 45 m2 Pa/W;
— Z2 ≤ 30 m2 Pa/W.
EN ISO 11092:2014, Textiles - Physiological effects - Measurement of thermal and water-vapour
resistance under steady-state conditions (sweating guarded-hotplate test)
Property | Pretreatment | Performance attribute 1 and Marking (where applicable) | Performance attribute 2 and Marking (where applicable) | ||
---|---|---|---|---|---|
Water penetration (Grade) | after | > 30 to ≤ 45 m2 Pa/W | Z1 | ≤ 30 m2 Pa/W | Z2 |
WHAT WE DO FOR
EN469 CERTIFICATION
Outer shell
- Flame & Heat Resistance
- Tensile & Tear Resistance
- Liquid Resistance
- Washable
- 6.2.1.1 Flame spread
- 6.2.1.6 Heat resistance
- 6.2.3.1 Tensile strength
- 6.2.3.2 Tear strength
- 6.2.5 Dimensional change
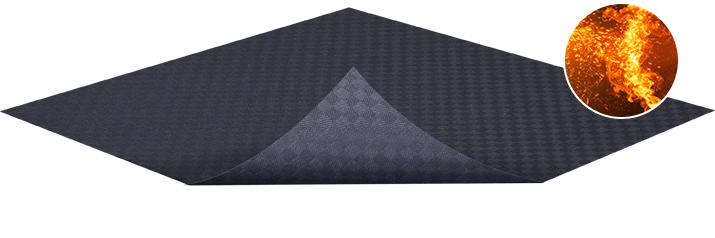
Moisture barrier
- Heat Resistance
- comfortable
- Washable
- 6.2.1.1 Flame spread
- 6.2.1.6 Heat resistance
- 6.2.5 Dimensional change
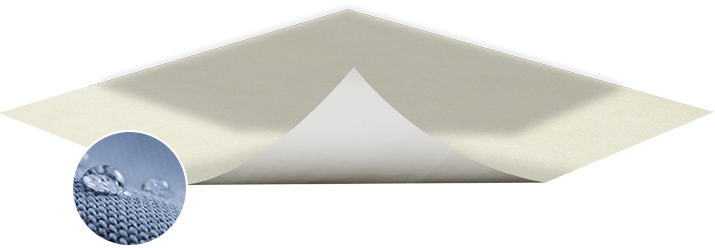
Thermal lining
- Moisture Resistance
- Vapour Resistance
- Virus & Blood Resistance
- Washable
- 6.2.1.6 Heat resistance
- 6.2.4 Water penetration
- 6.2.5 Dimensional change
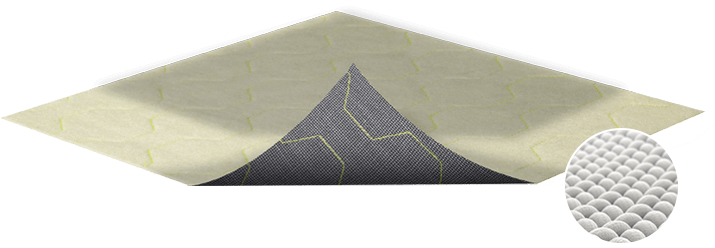
Combination
- 6.2.1.2 Contact heat
- 6.2.1.3 Heat transfer (flame)
- 6.2.1.4 Heat transfer (radiation)
- 6.2.1.5 Residual tensile strength
- 6.2.2 Resistance to penetration of chemicals
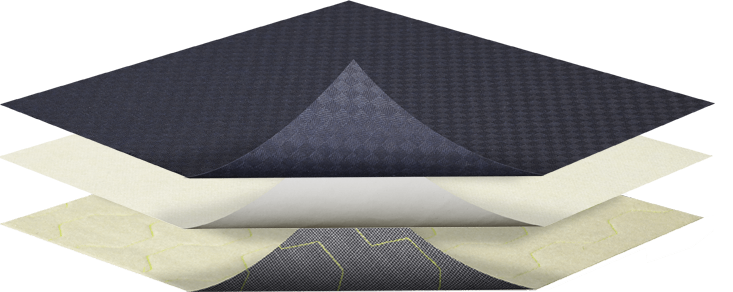
MODULE D
QUALIFICATION
Manufacturer shall operate an approved quality system for production, final product inspection and testing of the PPE concerned shall be subject to surveillance by a EU Approved Body, in accordance with PPE Regulations (EU)2016/425.
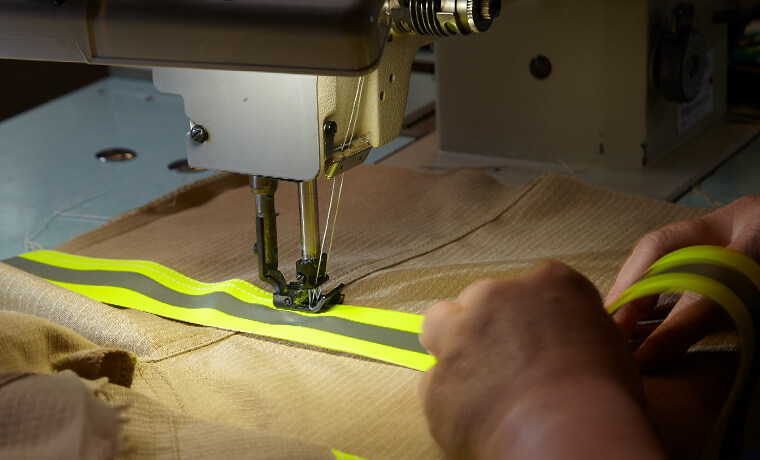
Module D audit procedures cover following:
- All of the manufacturer’s production sites;
- All of the manufacturer’s products and technical files;
- All of the manufacturer’s Module B Certificates
SUPER ARMOR adopt the strictest QA system for the production site and the office area, in order to ensure that the quality before, during and after the production process is consistent and exceeding the requirement of related harmonized standards
SUPER ARMOR adopt the strictest QA system for the production site and the office area, in order to ensure that the quality before, during and after the production process is consistent and exceeding the requirement of related harmonized standards
Premium Product to
Worldwide
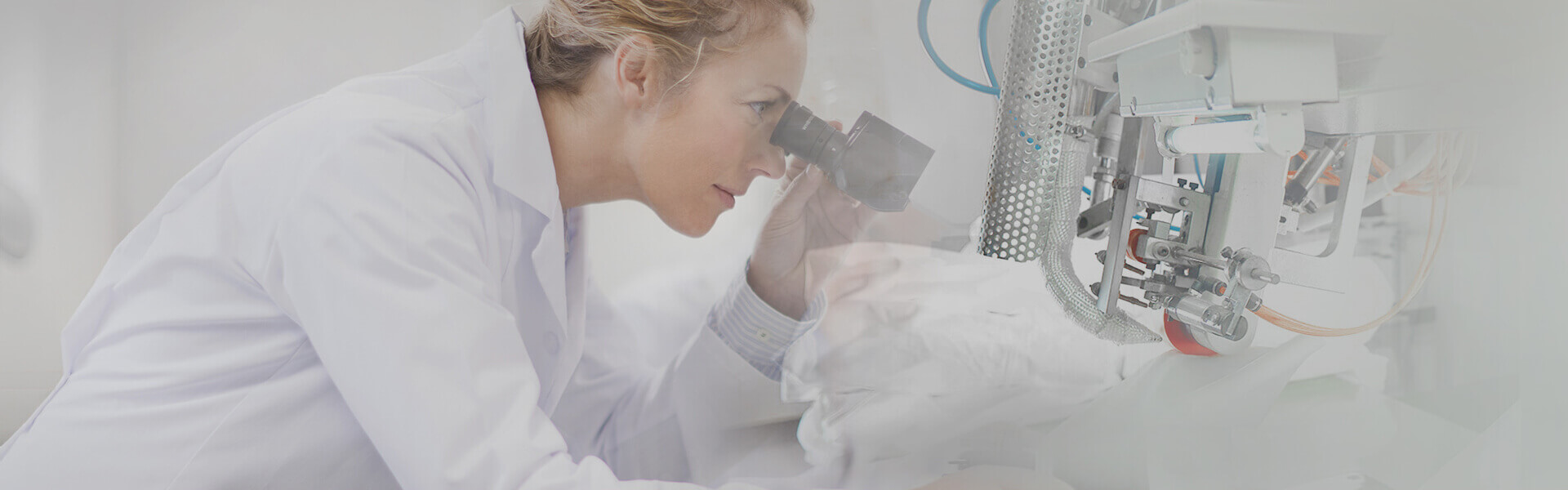